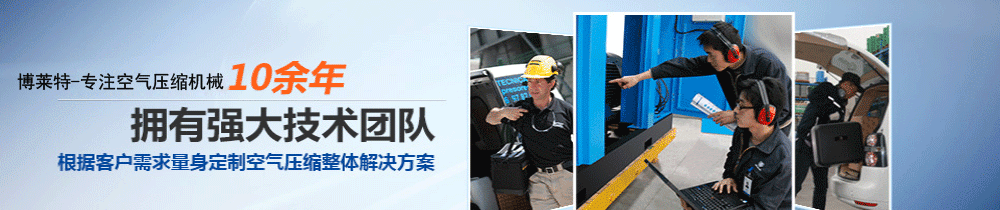
螺桿空壓機系統流程和各個零部件功能介紹
螺桿空壓機系統流程和各個零部件功能介紹
一.概述
壓縮機組為封閉箱式結構,包括壓縮機、傳動系統、進排氣系統、冷卻潤滑系統、控制系統及電氣線路組成,所有部件均裝在高強度結構底座上。
二.傳動系統
傳動系統由電動機通過皮帶或齒輪驅動壓縮機主機運轉,冷卻風扇由單獨的風扇電機帶動。
三.進排氣系統
空氣由空氣濾清器去塵埃后,經由進氣閥進入主機壓縮室進行壓縮,并與潤滑油混合.壓縮后的混合空氣進入油氣桶進行初分離,初分離后的混合空氣進入精密油氣分離芯進行精密分離后經最小壓力閥,進入后冷卻器,然后由出口閥進入用氣管路。
1.主要零件功能說明:
1.1 空氣濾清器
空氣濾清器為干式重載紙質過濾器,通常每1000小時應取下清除表面的灰塵,清除的方法是將灰塵由內向外吹除.
1.2 進氣閥
活塞式進氣閥工作原理:利用活塞前進與后退的動作來做空重負荷的控制。從星形相位進入三角形相位時,控制器將打開常閉電磁閥,壓縮空氣推動活塞后退,打開進氣閥,壓縮機進入滿負荷狀態,當達到額定壓力時,控制器將關閉常閉電磁閥,壓縮空氣推動活塞前進,關閉進氣閥,壓縮機進入空負荷狀態,并通過卸放閥放空。
蝶閥式進氣閥工作原理:壓縮機起動時,進氣閥閥片關閉,確保不帶負荷起動。空壓機加載時,三向電磁閥打開,由三向電磁閥通入氣體進入進氣閥的伺服氣缸,推動伺服氣缸的閥桿,帶動進氣蝶閥,使之全開,使空壓機加載。當系統壓力因用氣量減少而升高,達到反比例閥的設定壓力時,反比例閥動作并減少控制空氣輸出量,故進氣閥的伺服氣缸閥桿推動力減少,在彈簧力作用下,閥桿回縮,當彈簧力與氣缸的氣體推力平衡時,閥桿即處于半開狀態,此時,與閥桿相連的進氣閥片也處于半開狀態,進氣量即減小至與系統用氣量相平衡,此為容量調整過程。
若系統用氣量減少甚多,壓力上升速度超過容量調節的反應能力,則壓力開關動作,使電磁閥失電關閉,閥桿在彈簧的作用下,回到氣缸的底部,進氣閥片處于全關狀態,同時空壓機系統內的壓力經由泄放閥排空,主機處于空載狀態。當系統壓力下降至設定值時,控制器使電磁閥得電,恢復至加載狀態。
1.3 壓縮機主機
采用進口主機,為雙螺桿式壓縮機。進氣口位于機殼上部,排氣口位于機殼下部,一對高精密度陰陽轉子平行安裝于機殼內部。
1.4 油氣桶
油氣桶為潤滑油的貯油裝置,同時也是油氣混合氣的初分離裝置。壓縮空氣進入油氣桶,通過撞擊、旋風分離、流速降低等步驟;可使較大的油滴分離
1.5 安全閥
在壓力傳感器失靈而使油氣桶內的壓力比額定壓力高10%以上時,安全閥開啟,使壓力降至設定排氣壓力以下,對整個系統起到保護的作用。安全閥在出廠前已經過調定,請勿隨意調整。
1.6 精密油氣分離芯
深度型油氣分離芯,由多層微米級的玻璃纖維制成。壓縮空氣通過分離芯后,大部分的油都被分離出來,壓縮空氣的含油量可達到3ppm以下。
1.7 最小壓力閥
位于油氣桶上部精密油氣分離芯出口處,開啟壓力設定約為0.45Mpa。當系統壓力達到該壓力時才開啟供氣。其功能主要為:在啟動時優先建立系統的循環壓力,確保機體的潤滑;保護精密油氣分離芯因壓力差太大而受損傷;降低流過精密油氣分離芯的空氣流速,提高油氣分離效果。
四. 冷卻潤滑系統
1.系統流程
潤滑油依靠系統壓力從油氣桶進入油冷卻器冷卻后再進入油過濾器濾去雜質后,分成兩路,一路由機體下端噴入壓縮室,冷卻壓縮空氣;另一路通到機體另一端,潤滑軸承組,然后隨壓縮空氣再進入油氣桶。分離出大部分的油后,其余的含油空氣進入精密油氣分離芯,分離出的油聚集于分離芯底部,由回油管排至機體低壓端。
2 主要零件功能說明
2.1 潤滑油
采用博萊特壓縮機專用潤滑油,閃點為257℃,傾點為-42℃,可在極其惡劣的氣候和溫度環境下(-5℃ 45℃)正常運行.
2.2 油冷卻器為鋁制風冷式冷卻器,由冷卻風扇將冷卻空氣抽入,通過冷卻器來冷卻潤滑油。
2.3 油過濾器采用精密過濾器,過濾精度在15μm以下,能確保潤滑油潔凈,對軸承和轉子有很好的保護作用。帶有壓差指示器,如果顯示油過濾器壓差過高,表明油過濾器阻塞,應及時更換油過濾芯。
2.4 冷卻風扇
冷卻風扇由單獨的風扇電動機帶動,冷風由機組外部吸入,通過冷卻器冷卻潤滑油及壓縮空氣后,熱風排出機組外。
采購:螺桿空壓機系統流程和各個零部件功能介紹
聯系博萊特
400-966-0620

傳真:021-67743036
郵箱:15001822509@139.com
工廠地址:
無錫新區長江南路
辦公地址:
上海市金山區興塔鎮興坊路959號